Benefits of an Air Audit
There are many benefits of an air audit. It offers a clear understanding of the efficiency and performance of a compressed air system, aiding in the identification of areas for improvement. Moreover, audits can uncover potential equipment issues, thereby preventing costly downtime and repairs. Ultimately, a compressed air audit not only enhances system reliability but also boosts productivity, ensuring that compressed air resources are used optimally to support various manufacturing processes.
Following the recommendations of an N2O2 air audit typically results in the audit paying for itself. The benefits of an air audit become evident as it leads to substantial cost savings.
Some of the specific areas that collectively provide these returns include:
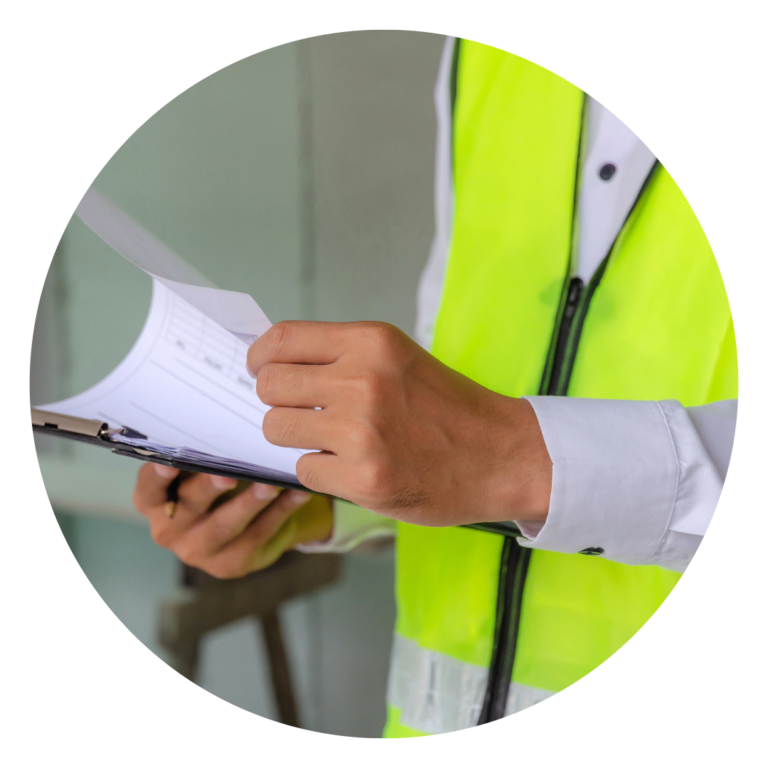
Operating a compressed air system at elevated pressures costs you money and often reduces the reliability of a compressed air system. Our clients often take the opposite approach, thinking that increasing system pressure will solve problems. Unfortunately with increased pressure, the leaks will leak more, and unregulated users will waste more air and more energy. However, lowering and controlling system pressure usually solves problems and increases plant reliability.
Improper application of storage tanks is a problem all too common in industry. Storage tanks by themselves often do not solve problems. In order for storage to provide benefit, pressure must be allowed to drop or fall, otherwise there is no storage in the system. On the contrary, by properly sizing, installing, and controlling storage, our clients often see big returns on investment.
In many compressed air systems, it makes sense to consider a compressor control strategy where the compressors control storage and the storage controls the system. This type of control and automation system usually keeps the minimum number of compressors running, which ultimately provides significant energy savings.
One of our strengths lies in our in-depth knowledge of compressed air drying and filtration. In many cases, we can deliver clients a substantial return on investment by meticulously designing and applying the appropriate technologies.
In many systems, it is possible to use “back pressure” steam turbine drivers in place of electric motors – for free! We have the background and ability to evaluate the potential use of steam drivers. When applicable, the ROI can be tremendous.
Intermittent compressed air demands like dense phase conveying, fermenters, baghouses, air horns, and many other applications, can be properly dealt with using storage and control. N2O2 has the knowledge and experience to convert these high demand, intermittent events, into low cost average compressed air consumers.
Be careful! Fixing air leaks by themselves does not always solve problems. Air leaks need to be considered in concert with the entire system and a plan to deal with them needs to be set up accordingly. N2O2 has the ability to conduct air leak audits. Leak audits are often most effective when conducted on a regular basis or in conjunction with a complete compressed air system analysis.
If air-operated pumps must be used, consider adding controls to shut the pumps off when they are not needed. Pumps waste the most air when they are pumping nothing. Also, check to see if the pump is running at the lowest possible pressure. Simple controls can increase pressure when needed. Lastly, investigate the use of electric motors to replace pneumatic pumps. The payback is often measured in months.
Vacuum audits can be considered together with a compressed air analysis, or separately. Our vacuum audits provide similar payback and ROI to our compressed air projects. Many times compressed air is used to generate vacuum. This in itself is an opportunity for efficiency gain.
We get hired for one of two reasons. One is to reduce energy. The second reason is when a system is out of control. When plant production and quality is sacrificed because of a poorly controlled and operated compressed air system, the improvements in compressed air efficiency can often dwarf the energy gains. The good news is our clients get both results at the same time – energy efficiency and improved reliability